The Process of Sampling and Testing and the Importance of Starting with Results in Mind
“The Process of Sampling and Testing and the Importance of Starting with Results in Mind” is a guest post by Jack van der Sanden, Senior Food Safety Advisor for bioMérieux. It explores why we sample and test and the significance of hygienic sampling, which is a critical component in ensuring the integrity of food samples and accurate microbial testing results. See the Author Bio at the end of the post.
In the world of food safety in the dairy industry, one of the key pillars is the process of sampling and testing. And we do test a lot! Starting on the farm, we test from the cows to the pens to the holding tanks and all the way to the tanker. Then at the dairy plant, we triple our testing by testing the raw milk, the environment, and then the final product before it leaves the dairy plant.
These sampling and testing activities are crucial in verifying that food safety and quality controls are working effectively. In this article, we will explore why we sample and test and the significance of hygienic sampling, which is a critical component in ensuring the integrity of food samples and accurate microbial testing results.
WHY Do We Sample and Test?
When I’m in a food factory, I often ask an operator, “Why do you take this sample and what are you looking for?” An easy enough question, but unfortunately, the most common answers are, “I don’t know, we have always taken this sample!” or “Because we have to!”
Sampling and testing are important expenses for a food business and the cost is often challenged during budget discussions because, “Surely, we do not need to test so many samples!” To answer this objection, we need to start with WHY.
You see, if we don’t have a clear WHY, the outcome of the budget discussion is that we often end up with a majority of “have to” samples, those samples that must be taken for compliance with regulatory, standard, and customer requirements. And guess what? As most of these compliance tests are finished product tests, the “have to” samples arguably have the lowest “utility value” for our business and miss the most important reason for sampling and testing: to verify that our food safety and quality controls are working.
Understanding the Role of Sampling and Testing
The Integrated Food Safety and Quality (FSQ) Pyramid below helps us understand the role of sampling and testing by answering:
- WHY we sample and test.
- WHY we need to invest time and effort in the design of our sampling plans for in-process, environmental, and finished product monitoring.
- WHY our results reporting needs to initiate the best possible management response.
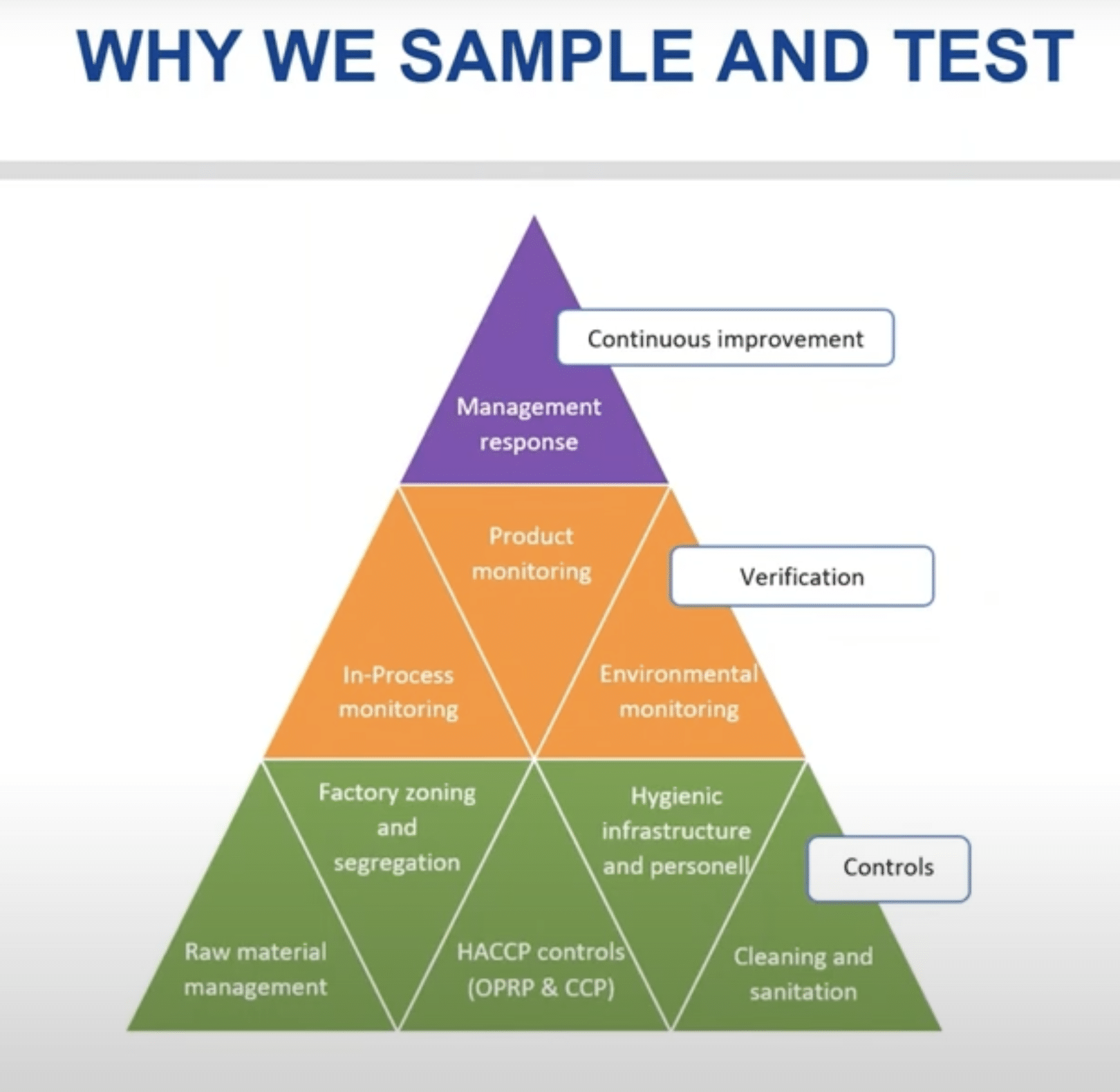
At the bottom of the FSQ Pyramid, we have the controls level, which are activities done by plant operators that produce good, safe products. These include:
- Manufacturing controls
- Quality controls
- Food safety controls
In the middle of the FSQ Pyramid sits the verification level to actually verify that the controls in the factory are working.
At the top of the FSQ Pyramid, we decide what to do with these verification results. These decisions drive continuous improvement when we use the verification results to improve our controls at the bottom of the FSQ Pyramid.
The Power of the Results
If a test result is in specification, then you most likely do not have a problem and the product is good to go. However, if the test result is out of specification, then decisions need to be made at the top of the FSQ Pyramid regarding what to do with the product and the next steps to take.
In my experience, when the result is out of specification, the immediate attitude is that there must be something wrong with the sample and a new sample is pulled. If you have a quality problem then it is likely the sample, but if it is a food safety issue that has resulted in an out-of-specification test result, then unfortunately, you cannot rely on a retest result to put you in the clear. An unexpected test result will highlight the importance of the sampling and testing process!
Introducing the SHACP
I have developed a tool I call the Sample Handling Control Points (SHACP), which stands for a combination of sampling and Hazard Analysis and Critical Control Points (HACCP), and enables us to review and improve the controls in our diagnostic chain. SHACP involves:
- Mapping the process
- Asking the questions
- Implementing controls
The Diagnostic Chain: Who Does What?
In the diagnostic chain, we start with the sampling plan. This could be either quality assurance (QA) or the manufacturing team that sets up the sampling plan. From there, the samples are taken by the operators and then transferred by someone to either an internal or external laboratory for testing and then the results go back to the manufacturing manager or the QA person.
The big issue here is that communication is not made easy due to the various parties involved in this diagnostics chain. For the purpose of this blog, we will focus on the Sampling Plan and Taking the Sample. Watch my sampling and testing webinar, The SHACP: Sampling Handling Control Points, for a deeper dive into the diagnostic chain.
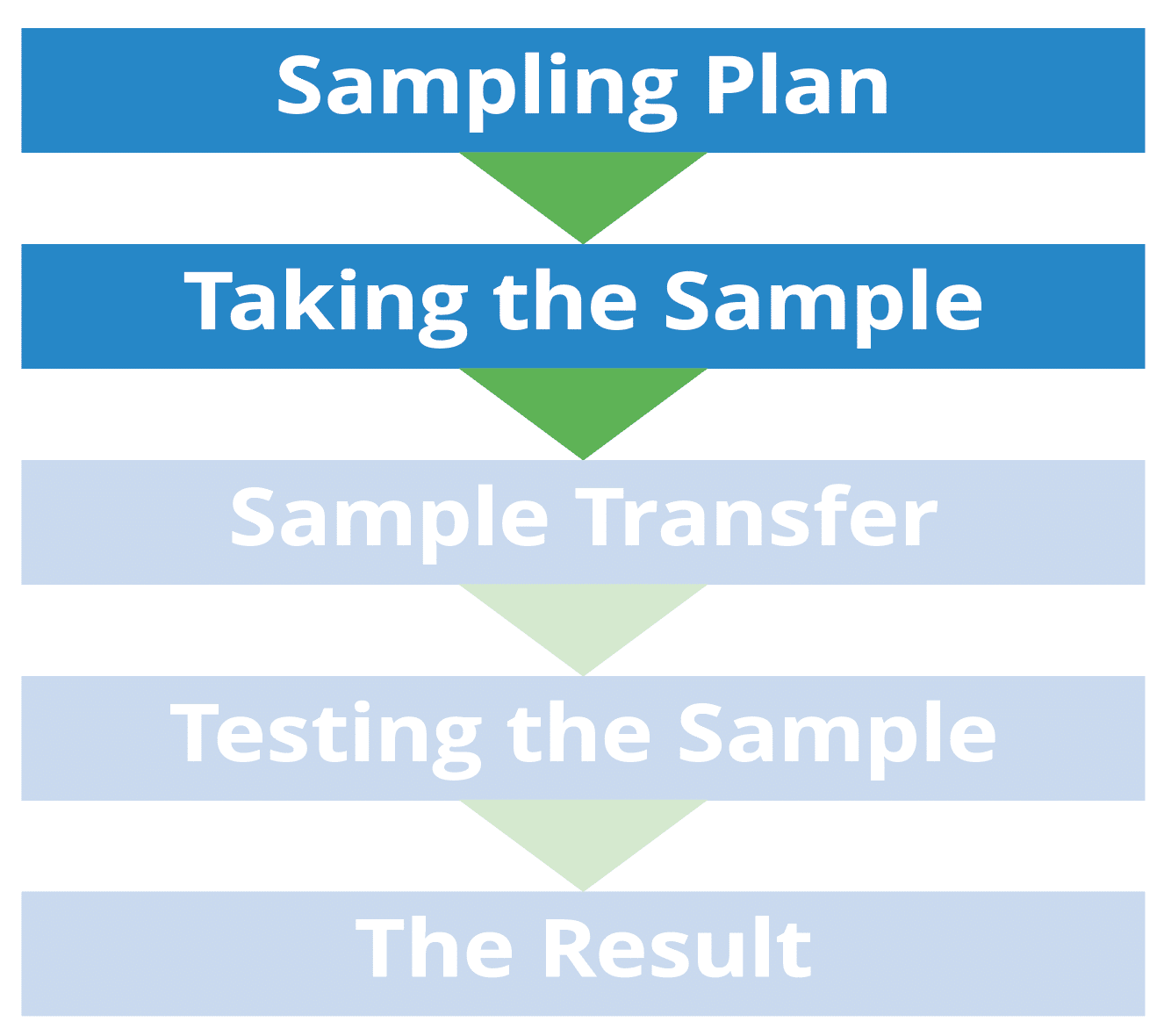
The Sampling Plan
One of the things I come across when I visit factories is that when I ask the question, “So why do you sample this?” and “Why do you take this sample?” one other common answer tends to be, “Well, because we’ve always done this and I think it’s important.” I’m not going to dive into this too deeply because that’s a separate topic, but you need to ask yourself some really good questions starting with, “Why do we do this?” Remember, it’s a fluid journey; it’s not fixed in time. You can adjust your sampling plan based on what you eventually find.
Taking the Sample: What Can Go Wrong?
If we dive deeper into taking the sample, the way that the SHACP works is that you ask the question, “What can go wrong?” The reality is, aseptic sampling is tricky and what can go wrong is that you can terminate your sample, which can then lead to invalid results from contaminants in the sample that are not truly in the process. So, the control really is to have a good look at your sampling equipment and use fit-for-purpose sampling equipment such as the QualiTru aseptic septum.
Sample and Test with the End Result in Mind!
You always need to sample and test with the end in mind. To do this, you need to really ask yourself two questions:
- What does this result tell me?
- What is the impact of this result if it is not what I expect?
When you take samples, it is important to spend the money needed to test those samples to obtain build results and data. Then when you take those results and data and put them into what I call an augmentation process and enhancement process, you may actually get some valuable insights that drive continuous improvements such as links, connections or correlations between different datasets within your business. Based on these insights, you can then actually optimize your clarification design or sampling plan, and you will have some form of prevention or predictive diagnostics.
Of course, it all starts with the sample.
And sample integrity ensures valid results.
And that, of course, drives continuous improvement.
Ask and Answer the WHY…
A robust verification process provides valuable feedback on our food safety and quality controls and improves our decisions. The verification process sits between the factory controls and our management response in the FSQ Pyramid. I cannot stress enough that you really want to ask and answer the question, “WHY do we sample?” Ensuring sure you ask and answer this simple question makes procedures and training much easier. If people know WHY they are sampling and testing, they will follow procedures. If people don’t know why they are sampling and testing, they will find (in their mind) a smarter way to solve a problem.
Finding solutions for contamination issues can be challenging, frustrating, time-consuming, and sometimes costly! If you have a contamination issue you are having trouble solving or would like to discuss a proactive process monitoring plan, contact us at (651) 501-2337 or complete our convenient “Ask Our Experts” form to have one of our customer representatives contact you.
Additional resources related to why we sample:
Articles
Sampling: Back to Basics
Improve the Sampling Process – Think SHACP
Related Blog Posts:
Hygienic Sampling Practices Are Vital to Protecting Dairy Product Quality and Safety
Post-Pasteurization Contamination Monitoring: A Canary in the Coal Mine
The Sample – Our Weakest Link!?
On-demand Webinar
Think SHACP: Sample Handling Control Points