Preventive and Predictive Maintenance: What is the Difference?
In the rapidly evolving landscape of the liquid food industry, maintenance strategies play a pivotal role in ensuring operational efficiency, product quality, and safety. Among these strategies, preventive and predictive maintenance stand out as two fundamental approaches, each with its distinct methodology and impact on the production lifecycle. Understanding the nuances of the these maintenance strategies and the role of aseptic sampling is key to enhancing predictive maintenance practices.
Understanding Preventive and Predictive Maintenance Strategies: Scheduled vs. Data-Driven
Preventive maintenance refers to the scheduled maintenance activities performed on machinery and equipment to prevent unexpected failures. This strategy is based on a time or usage schedule, ensuring that maintenance tasks are carried out at regular intervals, irrespective of the equipment’s current condition. The primary goal is to minimize the risk of equipment failure and maintain consistent production quality. However, this approach can lead to either unnecessary maintenance tasks or overlook potential failures not aligned with the maintenance schedule.
Predictive maintenance, on the other hand, represents a more data-driven approach that is characterized by its use of condition-based monitoring (CBM), prognostics and health management (PHM), and estimation of the remaining useful life (RUL) of equipment. This approach relies heavily on data collected from various sensors installed on the equipment, which is then analyzed using machine learning models to predict when a piece of equipment is likely to fail or require maintenance. The core advantage of predictive maintenance over traditional preventive maintenance is its ability to minimize unnecessary maintenance activities, reduce operational costs, and ensure uninterrupted production processes, which is critical in the highly regulated liquid food industry (Achouch et al., 2022).
Key Differences in Preventive and Predictive Strategies
Maintenance Scheduling: Preventive maintenance operates on a fixed schedule based on time or usage, whereas predictive strategies rely on real-time data and predictive analytics to determine when maintenance is needed.
Cost Efficiency: By focusing on actual equipment conditions, maintenance can be more cost-effective, reducing unnecessary tasks and ensuring resources are used where they are most needed.
Operational Efficiency: Predictive maintenance aims to minimize unplanned downtime by predicting failures before they happen, whereas preventive maintenance follows a set schedule, which may not always align with the equipment’s actual condition.
Quality and Safety: Integrating aseptic sampling solutions with predictive methods can enhance product quality and safety by ensuring that maintenance decisions consider the product’s microbial and chemical integrity.
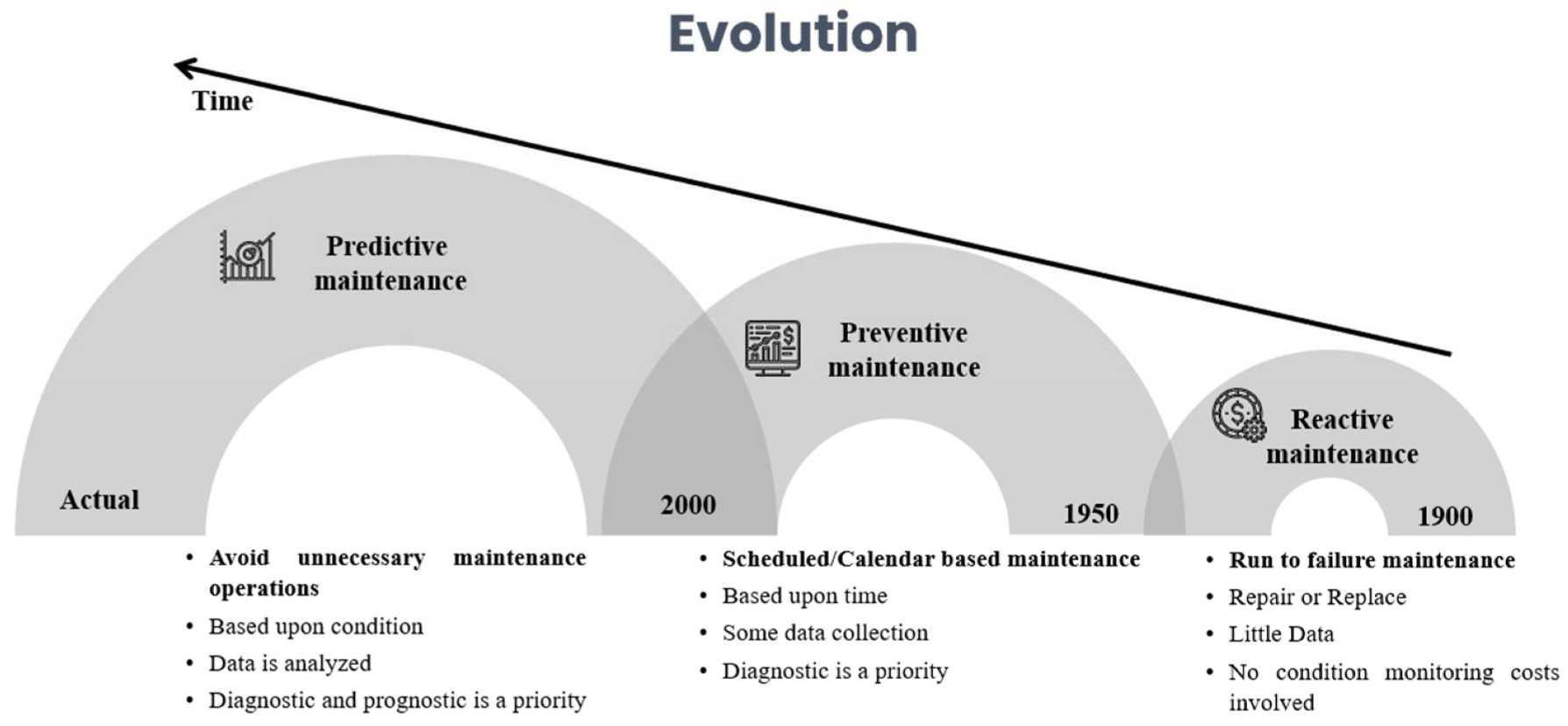
The Importance of Aseptic Sampling for Effective Maintenance
In the liquid food industry, product quality and safety are critical. Aseptic sampling solutions are essential tools that provide precise, real-time data on microbial and chemical levels in products, supporting various maintenance strategies. By combining aseptic sampling with advanced monitoring technologies, companies can gain a deeper understanding of their equipment’s condition, leading to better maintenance decisions. This enhanced insight helps improve product quality and safety by allowing timely interventions and reducing risks associated with contaminated products or equipment failures.
Leveraging QualiTru Sampling Systems for Quality and Efficiency
Choosing between these two maintenance strategies depends on various factors, including the specific needs of the production facility, the complexity of the machinery, and the criticality of maintaining product quality and safety. Predictive maintenance, supported by QualiTru aseptic sampling systems, helps ensure maintenance strategies that provide a data-driven, efficient, and effective approach to equipment maintenance and product safety.
Discover the QualiTru difference. Optimize your operations, reduce downtime, and maintain the highest standards of product quality and safety across the dairy, brewery, beverages and liquid foods, biofuels, enzyme manufacturing, and nutraceutical and functional foods industries with QualiTru. Visit QualiTru Sampling Systems today to learn more about how our aseptic sampling solutions can transform your maintenance strategy and help you stay ahead in the competitive liquid food industry.
References
Achouch M, Dimitrova M, Ziane K, Sattarpanah Karganroudi S, Dhouib R, Ibrahim H, Adda M. On Predictive Maintenance in Industry 4.0: Overview, Models, and Challenges. Applied Sciences. 2022; 12(16):8081. https://doi.org/10.3390/app12168081
Additional QualiTru blogs by Neil Bogart
If you’re looking for additional expert insights into micro testing, dairy industry practices, and food safety, don’t miss additional blog posts by Neil Bogart on the QualiTru Sampling Systems website. Neil brings a wealth of knowledge and experience to each article, offering practical advice and in-depth analysis on various topics related to quality assurance and innovative solutions in food production.
Have questions about aseptic sampling in breweries?