Aseptic and Representative Sampling for Dairy Plants
Aseptic and representative sampling for dairy plants must meet a variety of needs and applications. QualiTru’s sampling solutions are simple to use and provide easy access throughout the dairy processing plant, allowing for comprehensive quality assurance.
Maintaining high quality is essential for dairy processors to remain competitive, improve profitability, and establish or maintain a strong foothold in domestic and international markets. Failure to maintain dairy quality can lead to economic losses, reduced competitiveness, and potential damage to a company’s reputation.
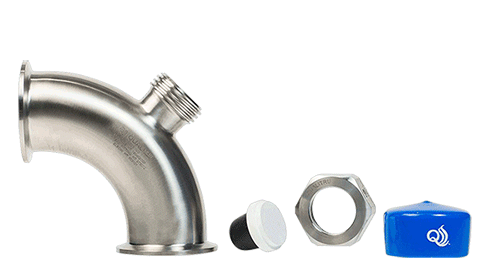
QualiTru Can Help Optimize Quality Management
The quality of finished dairy products starts on the farm and carries through processing. A well-conceived quality assurance program will aid profitability by ensuring good quality raw milk supplies and ingredients, catching post-pasteurization contaminants before they can inflict damage to revenue or brand reputation, uncovering hidden problems with processing procedures or equipment, and assessing the efficacy of hygiene programs.
Value proposition:
Problems we solve:
QualiTru’s applications and solutions for dairy plants:
Have questions about aseptic and representative sampling?
Need a quote? We’ll respond to
your request quickly.
Looking for one of our global distribution partners near you?
Implementing Innovative Practices for Improved Milk Quality
Maintaining the microbiological quality of dairy is challenging, and process monitoring is a critical element. Microbiological sampling at CCP in the process helps dairy farm managers control contamination, validate cleaning and sanitation procedures, and identify sources of raw milk contaminants. QualiTru TruStream™ devices are ideal for sampling at these critical locations.
Sampling Site Recommendations: Aseptic and Representative Sampling for Dairy Plants
.
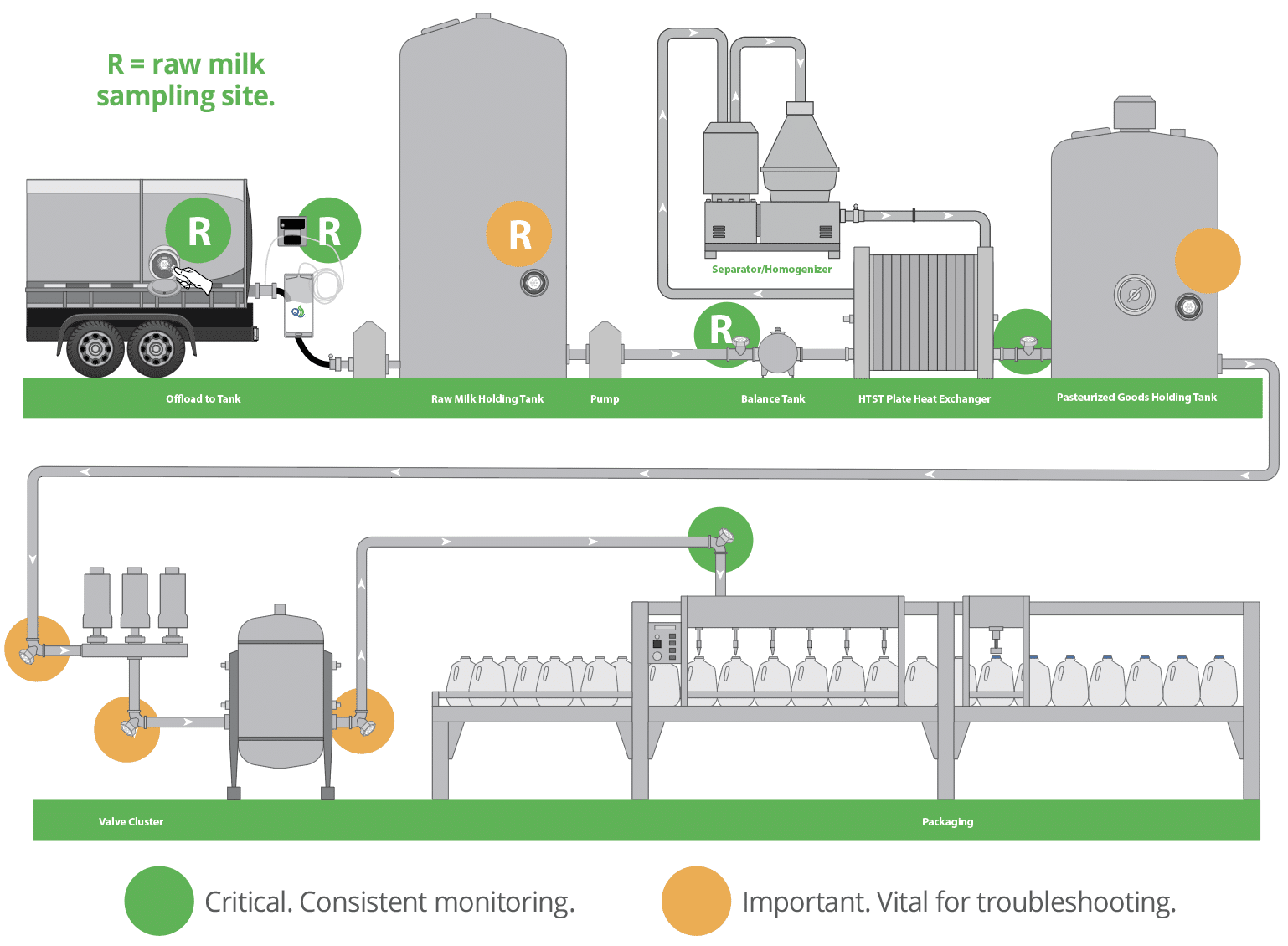
Most critical (Green): These are the most essential steps in the process that need consistent monitoring:
- Raw milk received at the processing plant can be sampled directly from the tanker using a TruDraw® collection vial and/or, more appropriately, a larger sample should be collected using a TruMotion 2 liter Collection Bag and Watson-Marlow peristaltic pump as the milk is being offloaded from the tanker. Test results on these samples are used to i) determine if the raw milk is of sufficiently high quality for acceptance by the plant; ii) determine the level of thermoduric organisms, such as spore formers, that may survive pasteurization and contaminate finished product; and iii) provide a baseline as comparison with further tests.
- Raw milk from the balance tank of the pasteurizer should be sampled using a TruDraw collection vial injected through a TruStream sampling device positioned immediately ahead of the balance tank. Test results on these samples will be compared with those taken off the milk transport (above) and those at the high-temperature short-time (HTST) pasteurizer’s discharge.
- The HTST pasteurizer should be sampled at its discharge. Samples from this location should be free of bacteria unless there are thermoduric lactic acid bacteria in the milk surviving pasteurization or the pasteurizer is contributing post-pasteurization contaminants from the cooling section. Tests from these samples should be carefully analyzed for Gram-positive spore formers, Gram-positive lactic acid bacteria, Gram-negative psychrotrophic bacteria, and coliforms using the appropriate analytical techniques.
- Immediately before each filling machine is the final process CCP before the finished product. Testing at this location isolates the entire process from the discharge of the pasteurizer to the filling machine and, by exclusion, isolates the filling machine. Test results from this location should be compared to those from the pasteurizer discharge and to tests performed on finished packages. If the total bacteria or coliform count from these samples is higher than the results from the HTST discharge, then post-pasteurization contaminants are coming from somewhere in the process. If the test results from finished milk samples are higher than those taken immediately before the filling machine, then the filling machine is contaminating the finished product.
Vital for troubleshooting potential sources of contamination (Gold): Sampling points shown in gold require monitoring if troubleshooting for post-pasteurization contamination becomes necessary. Ideally, sample collection ports should be installed in each raw and pasteurized milk holding silo; before and after each mixing or blending tank; before and after each valve cluster; and before and after each additional piece of equipment that may be in the process. This process allows each piece of equipment to be isolated and clearly shows where the post‑pasteurization contamination originates.
The journey towards exceptional dairy product quality begins at the farm and continues throughout the processing chain. QualiTru’s aseptic sampling systems deliver a reliable and efficient means for dairy plants to monitor milk quality for contaminants. By facilitating accurate, timely, and reliable sampling, QualiTru systems enable proactive interventions, helping to maintain the highest standards of dairy product safety and quality.
- Inline Sampling
- TruStream7 Tri-Clamp Tee 2” (Part # 215147) or TruStream 7 Tri-Clamp Elbow 2″ (Part #213029)
- TruStream7 Septa (Part # 110011)
- TruStream 250ml/18g (Part # 111450) for a representative sample or the TruDraw® Sterile Single Sampler (Part #112021) for a small, aseptic sample
- Holding Tank Sampling
- TruStream7 Recessed 4”x 2” (Part # 212123)
- TruStream7 Septa (Part # 110011)
- TruDraw® Sterile Single Sampler (Part # 112021)
(Click on thumbnails to view larger photos)
Meeting the challenges of dairy plants
Our sampling system is easy as 1-2-3-4
Since 1983, the dairy industry has relied on QualiTru® Sampling Systems to provide fast, simple, safe, and accurate samples for bacterial and chemical quality analysis. A low cost per sample allows QualiTru’s sampling systems, such as the TruStream Septa and TruStream Ports, to be used widely on the farm and at every step in processing to help ensure the consistently high-quality inline process monitoring needed in today’s dairy processing environment.
Interesting facts about the dairy industry
Dairy farmers commit their lives to feeding the world.
The entire dairy industry, from farm to manufacturer, contributes less than 2% of total U.S. GHG (Greenhouse Gas) emissions.
(Source: Dairy Farmers of America)
The U.S. dairy industry now contributes:
- 3.5 percent of U.S. GDP
- 3.3 million total jobs
- $41.6 billion in direct wages for workers
- $67.1 billion in federal, state, and local taxes
(Source: International Dairy Foods Association)
To learn more about our aseptic and representative sampling solutions for dairy plants, please call
651-501-2337 or email us at [email protected]